Planned Preventative Maintenance schedules – All assets and MEP and Drainage systems
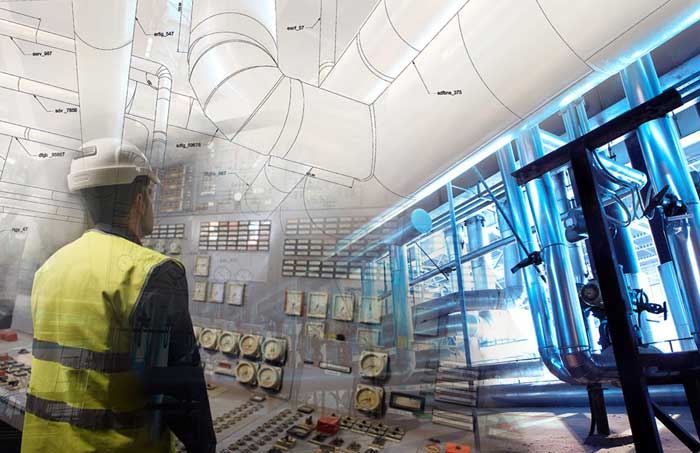
- Maintenance of all assets at best performance levels, as per Corporate specs and recommendations made by local professional bodies that include all statutory requirements.
- Provide necessary support to any type of Business Contingency Plan situation as directed by the client
- Timely identification and rectification of faults that are recorded, are time-bound and shared to facilitate quality analysis.
- Statutory inspections with comprehensive inspection programmers in accordance with industries’ best practices.
- Periodical review on condition of premises and equipment’s covered within the contract ex: Electrical equipment and systems, Mechanical equipment and systems, Plumbing systems, Building Fabric, External Areas, Fixtures and fittings
Breakdown Maintenance
Planned Preventative Maintenance schedules – All assets and Mechanical, Electrical, Plumbing and Drainage systems
- Reduce Downtime
- Failure Analysis
- Recording events
- Refer Case studies/ Best Practices as preventive measures
Preventive Maintenance
- Reduction of equipment down time.
- Higher operating efficiencies
- Extended life time of equipment’s
- Protection against unexpected failures
- Historical logs of equipment condition and service
Routine Maintenance
- A daily site walks to check the engineering systems and plant rooms.
- Maintain records and escalate abnormalities.
- Weekly visual check on architectural and building services installations.
- Immediate repairs as required
- Records of visual check results with recommendations and implementation of appropriate solutions
Building Management Solutions
AGS operates Building Management Systems that comprise of Access Control, CCTV, Fire Alarm and Building Automation Systems, for efficient functioning and security of the premises
HVAC (Operation & Maintenance)
- Operation & Maintenance of Centralised Chiller units including pumps & VFD’s
- Split / Package air- conditioners cleaning of filters, checking of wiring and plugs, testing of machine for proper operation and signs of wear & tear
- Regular checking & periodic cleaning of equipment such as FCU, AHU and ventilation fans, etc.
- Checking of fire dampers in ventilation ducts is checked on a regular basis.
- Check Preventive maintenance which is not under the AMC.